In the digital of industrial machinery and equipment maintenance, the assessment of wear and tear plays a crucial role in ensuring operational efficiency and longevity. Among various methods of inspection, one significant phenomenon that warrants attention is pitting, particularly concerning the Vt1000—a widely used model in various sectors. This article delves into the importance of Vt1000 pitting photo examples, providing a comprehensive understanding of the issue, its implications, and the benefits derived from recognizing and addressing pitting early on.
What Is the Dekra VT1000?
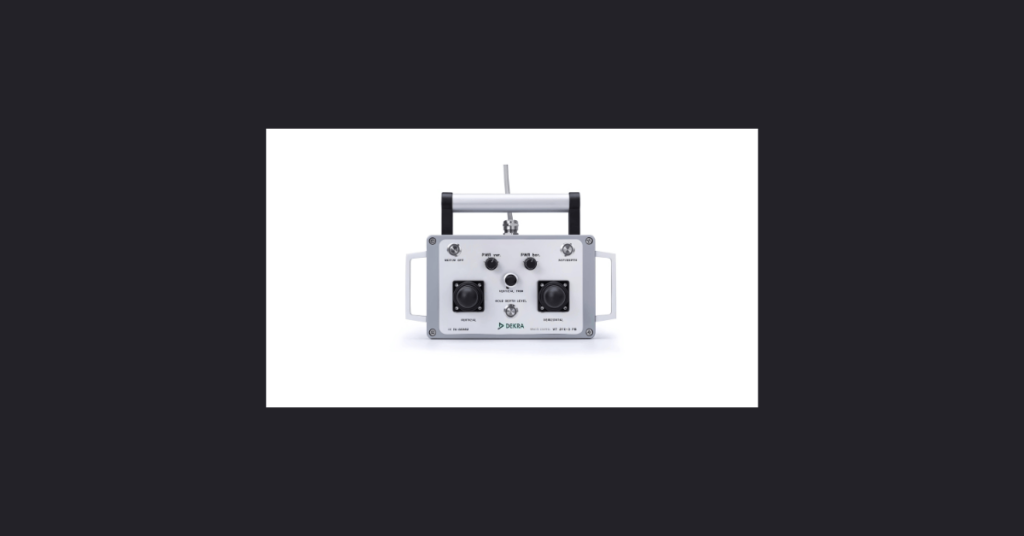
A cutting-edge inspection instrument for spotting corrosion, especially pitting in a variety of materials, is the Dekra VT1000. Due to its high-resolution imaging capabilities, even the smallest indications of pitting corrosion can be identified by using the precise visual data that it can capture of metal surfaces. This cutting-edge system finds extensive application in the oil and gas, aerospace, and industrial industries, where corrosion detection at an early stage is critical to preserving equipment structural integrity.
Understanding Pitting in the Context of Vt1000
Pitting is a localized form of corrosion that results in the creation of small depressions or “pits” on a material’s surface, often affecting metals exposed to harsh environments. In the context of the Vt1000, which is utilized across different industrial applications, understanding the mechanics of pitting is paramount. Pitting can arise due to various factors, including but not limited to electrochemical reactions, mechanical wear, and environmental conditions. These pits can compromise the structural integrity of components, leading to failure if not properly managed.
Read More: singer 221k ev909542
Key Features of the DEKRA VT1000
- High-Resolution Imaging: The VT1000 uses state-of-the-art cameras and sensors to capture detailed images of vehicle components.
- Advanced Software Analysis: Along with photos, the system includes software that analyzes the images, highlighting potential issues.
- Comprehensive Reporting: The tool generates detailed reports that can be shared with mechanics, fleet managers, or safety inspectors for immediate action.
- User-Friendly Interface: Easy to use, even for non-technical users, ensuring inspections are performed quickly and accurately.
These features combine to make the VT1000 not just a diagnostic tool but a complete solution for vehicle safety management.
Why Are Pitting Images Important?
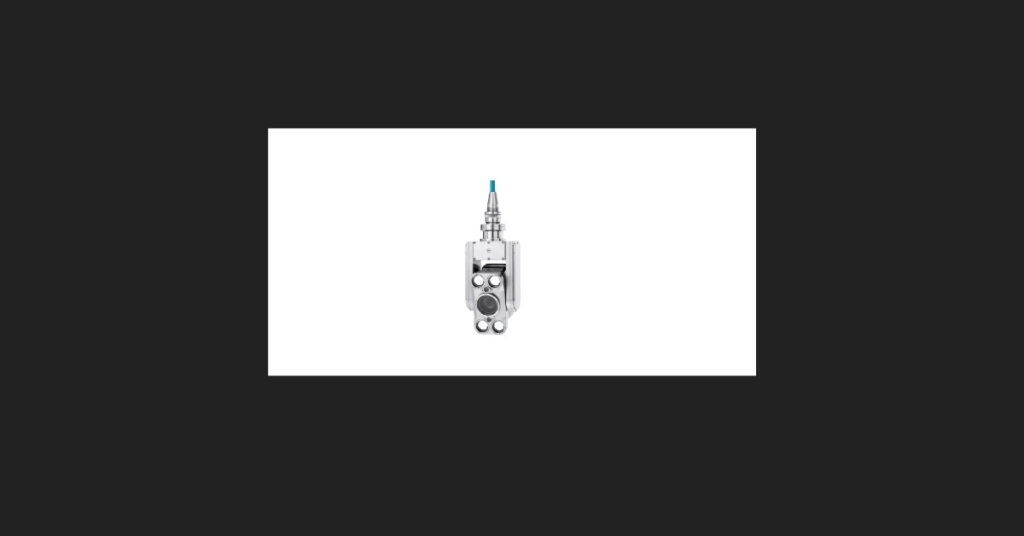
Pitting images provided by the DEKRA VT1000 are essential for spotting early signs of wear that might be invisible to the naked eye. These images facilitate thorough inspections, helping identify potential issues before they escalate. For example, pitting on brake discs can impair braking efficiency, increasing the risk of accidents.
Utilizing these images allows fleet managers, mechanics, and drivers to better assess the vehicle’s condition and take proactive measures to repair or replace parts as needed.
Importance of Pitting Corrosion Detection
Detecting pitting corrosion through the DEKRA VT1000 is critical for:
- Preventing Failures: Early detection can prevent catastrophic failures in critical structures.
- Extending Lifespan: Regular inspections can prolong the life of materials and reduce maintenance costs.
- Ensuring Safety: Identifying defects helps maintain safety standards in various applications.
The Dekra VT1000 Pitting Images
Pitting corrosion affects metal surfaces, and the Dekra VT1000 is particularly successful in capturing detailed photos of those surfaces thanks to its unique features. It is among the greatest instruments for corrosion detection accessible for a variety of applications because of its capabilities, which go beyond simple inspections.
Understanding ATEX Zone 1 Ensuring Safety in High-Risk Environments
Areas, where explosive atmospheres are likely to occur regularly under typical operational conditions, are designated as ATEX Zone 1. This categorization is important for areas where, in the course of daily activities, air may come into contact with combustible materials such as fumes, vapors, or dust. These risks are frequently encountered by sectors including chemical processing, oil and gas extraction, and pharmaceutical manufacturing. All equipment in these high-risk environments needs to be carefully constructed to eliminate any chance of igniting, protecting personnel and procedures alike.
The Crucial Role of Specialized Cameras in ATEX Zone 1
Conventional cameras are inadequate in ATEX Zone 1 conditions, where safety is of utmost importance and even the smallest mistake can have catastrophic effects. These common cameras are dangerous because they can produce heat or sparks that could ignite dangerous environments. Because of this, specific equipment is needed to guarantee both functionality and safety in these high-risk situations. One of the best examples of this specialized technology is the pitting inspection camera, DEKRA VT1000. Specifically engineered to meet the strict safety regulations for ATEX Zone 1, the DEKRA VT1000 is equipped with innovative technologies that considerably limit the risk of fire. Its sturdy build and innovative design allow it to function safely in dangerous environments and produce sharp, high-quality photographs.
Manufacturing Sector

Because of its frequent use, manufacturers rely on equipment that is prone to pitting corrosion. By enabling early corrosion detection on vital components like gears and valves, the DEKRA VT1000 helps to avert unplanned equipment breakdowns. Businesses can plan for timely maintenance, save production delays, and increase the lifespan of their gear by detecting wear before it results in breakdowns. Additionally, the VT1000 allows for more accurate repairs, which lessens the need for expensive part replacements.
Future Trends in Pitting Detection and Management
As industries continue to evolve, so too do the methodologies employed for managing equipment wear, including pitting. The future of pitting detection and management is likely to be shaped by ongoing advancements in technology and data analytics. Predictive maintenance, powered by machine learning algorithms, offers the promise of identifying potential issues before they manifest as significant problems.By analyzing data gathered from sensors and imaging technologies, organizations can establish patterns that indicate when and where pitting is likely to occur. This predictive approach not only aids in timely intervention but also optimizes maintenance schedules, ensuring that resources are allocated efficiently.
FAQs
What is the DEKRA VT1000 used for?
The DEKRA VT1000 is an advanced inspection tool designed for detecting corrosion, especially pitting, on various materials in industrial settings.
How does pitting affect equipment performance?
Pitting creates small depressions on metal surfaces that can compromise structural integrity, leading to failures in critical components and decreased operational efficiency.
Why are pitting images important in maintenance?
Pitting images help identify early signs of wear that are not visible to the naked eye, enabling proactive repairs and preventing catastrophic failures.
What industries benefit from using the DEKRA VT1000?
Industries such as oil and gas, aerospace, and manufacturing benefit significantly from the DEKRA VT1000 for its ability to detect corrosion early and enhance equipment safety.
How does the DEKRA VT1000 ensure safety in ATEX Zone 1 environments?
The DEKRA VT1000 is specifically designed to meet safety regulations for ATEX Zone 1, minimizing fire risks while providing high-quality imaging in hazardous conditions.
Ending Point
The DEKRA VT1000 is an essential tool for early detection of pitting corrosion, enhancing safety and operational efficiency across various industries. By leveraging advanced imaging technology, organizations can proactively address wear and tear, ultimately extending the lifespan of critical equipment.
Stay Connected: Bossip.blog